Understanding the Importance of Regular Asset Inspections to Avoid Expensive Repairs
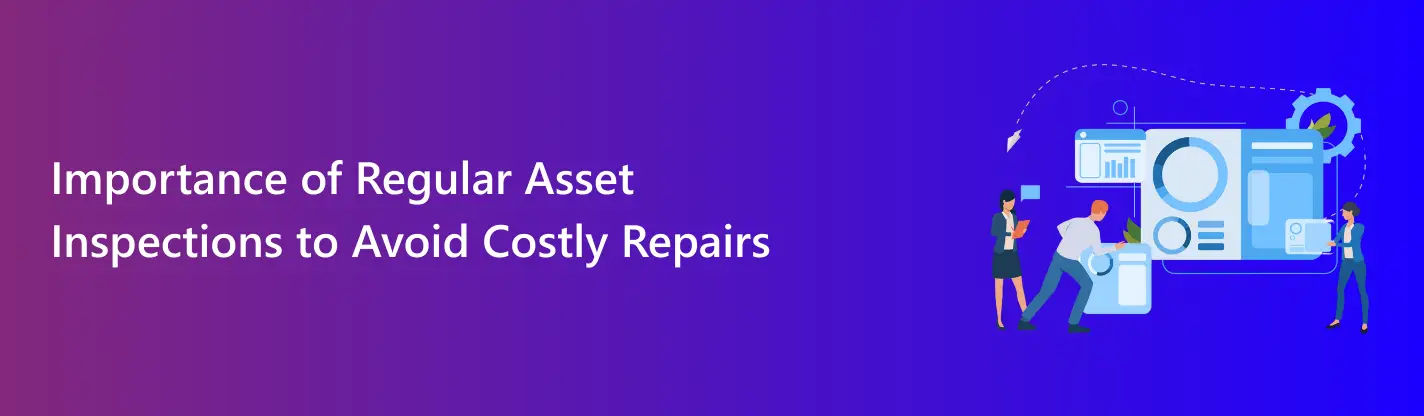
Your assets—whether they’re machines, vehicles, buildings, or equipment—are the backbone of your life or business. But like anything valuable, they need to care to keep working well. Ignoring them can lead to breakdowns, safety risks, and costly repairs that hit your wallet hard. Regular asset inspections are the key to catching small problems before they turn into big ones.
This blog explains why inspections matter, how to do them right, and how they save you money in the long run.
What Are Asset Inspections?
Asset inspections are routine checkups to make sure your stuff is in good shape. Think of them like doctor visits for your equipment or property. You’re looking for signs of wear, damage, or anything that could cause trouble later. Assets can include:
- Machines: Factory equipment, forklifts, or conveyor belts.
- Vehicles: Cars, trucks, or construction gear like bulldozers.
- Buildings: Roofs, HVAC systems, or plumbing.
- Tools: Smaller items like power drills or safety gear.
Without regular inspections, small issues—like a loose bolt or a tiny leak—can grow into major problems, leading to downtime, accidents, or expensive fixes.
Why Regular Inspections Are a Big Deal
Skipping inspections might seem like a time-saver, but it’s a gamble that can cost you. Here’s why regular checkups are so important:
- Catch Problems Early: A small crack in a machine part can become a full breakdown if ignored. Inspections spot these issues before they escalate.
- Save Money: Fixing a minor leak is way cheaper than replacing a flooded engine. Early repairs keep costs low.
- Avoid Downtime: Broken assets can halt work, costing you time and productivity. Inspections keep things running smoothly.
- Improve Safety: Faulty equipment or building systems can hurt people. Regular checks reduce risks and keep everyone safe.
- Meet Rules: Many industries have laws requiring inspections. Skipping them can lead to fines or legal trouble.
- Extend Asset Life: Well-maintained assets last longer, so you don’t have to replace them as often.
For example, a 2021 report found that unplanned downtime costs Fortune 500 companies up to $1.5 trillion a year. Regular inspections can prevent these losses by keeping assets in top shape.
Steps to Inspections Asset to Avoid Expensive Repairs
Step 1: Know Your Assets
To inspect your assets, you first need to know what you’re working with. Make a list of everything you own that needs checking.
How to Start:
- Create an Inventory: Write down all your assets, like machines, vehicles, or building systems. Include details like brand, model, and purchase date.
- Group by Type: Organize assets into categories, like “heavy equipment” or “electrical systems,” to make inspections easier.
- Track Usage: Note how often each asset is used and under what conditions (e.g., harsh weather or heavy loads). This helps you decide how often to inspect.
Tools to Help:
- Spreadsheets: Use Excel or Google Sheets to keep your list organized.
- Asset Management Software: Tools like UpKeep or FTQ360 can track assets and schedule inspections.
- Labels: Tag assets with IDs or QR codes for easy tracking.
Knowing your assets sets the foundation for a solid inspection plan.
Step 2: Set Up an Inspection Schedule
Inspections only work if you do them regularly. Create a schedule based on your assets’ needs and stick to it.
How to Schedule:
- Follow Manufacturer Guidelines: Check manuals for recommended inspection intervals (e.g., every 500 hours for a machine).
- Consider Usage: Assets used daily need more frequent checks than those used occasionally.
- Factor in Environment: Harsh conditions, like extreme heat or dust, mean more frequent inspections.
- Use a Calendar: Set reminders for daily, weekly, monthly, or yearly checks, depending on the asset.
Types of Schedules:
- Daily: Quick visual checks for high-use equipment, like looking for leaks or unusual noises.
- Weekly/Monthly: Deeper inspections, like testing controls or checking fluid levels.
- Yearly: Thorough reviews, often by professionals, for things like building roofs or HVAC systems.
Maintenance software can automate reminders, so you never miss a check.
Step 3: Use the Right Inspection Methods
Not all inspections are the same. Different assets need different approaches to spot problems.
Common Methods:
- Visual Inspections: Look for obvious issues, like cracks, rust, or worn parts. This is often the first step.
- Preventive Maintenance Checks: Test specific parts, like lubricating joints or calibrating gauges, to prevent wear.
- Functional Tests: Run equipment to ensure it works properly, like testing a vehicle’s brakes or a machine’s controls.
- Specialized Inspections: Use tools like infrared thermometers or vibration pens to detect hidden issues, like overheating or misalignment.
Tips for Effective Inspections:
- Use Checklists: Create a list of things to check for each asset, like fluid levels or safety features. This ensures nothing gets missed.
- Train Your Team: Make sure everyone knows how to spot problems and use inspection tools.
- Document Everything: Take notes, photos, or videos of what you find. This helps track issues over time.
Using the right methods catches problems early and keeps your assets in top condition.
Step 4: Act on What You Find
Finding an issue is only half the battle—you need to fix it before it becomes a bigger problem.
How to Follow Up:
- Prioritize Repairs: Fix safety hazards or critical issues first, like a broken guardrail or a leaking hydraulic system.
- Schedule Fixes: For non-urgent issues, plan repairs during downtime to avoid disrupting work.
- Record Actions: Log what you fixed and when, so you have a history of maintenance. This is also useful for audits or warranty claims.
- Communicate: If you’re part of a team, share findings with managers or coworkers to ensure everyone’s on the same page.
Software like SafetyCulture or Fieldwire can streamline this process by letting you assign tasks and track repairs.
Step 5: Protect Your Assets Between Inspections
Inspections are important, but what you do between them matters too. Proper care extends asset life and reduces repair costs.
Maintenance Tips:
- Clean Regularly: Dirt and debris can wear out parts faster. Clean machines, vehicles, or building systems as needed.
- Store Properly: Keep assets in dry, secure places to avoid rust or damage.
- Use Correctly: Train users to operate equipment properly to prevent misuse.
- Lubricate Moving Parts: Apply oil or grease to reduce friction and wear.
- Monitor Conditions: Check for signs of trouble, like strange noises or slow performance, and address them quickly.
Good habits between inspections keep your assets running smoothly and reduce the need for major repairs.
Step 6: Stay Compliant with Regulations
Many assets have to meet safety or industry standards. Regular inspections ensure you’re following the rules and avoiding penalties.
Key Regulations:
- OSHA: Requires regular checks for workplace equipment to ensure safety.
- EPA: Sets standards for assets like HVAC systems to protect the environment.
- Industry Standards: Groups like ASTM or API set rules for specific equipment, like construction gear or oil rigs.
How to Stay Compliant:
- Know the Rules: Research regulations for your assets, like OSHA’s heavy equipment standards.
- Keep Records: Save inspection reports and repair logs to prove compliance during audits.
- Hire Experts: For complex assets, bring in certified inspectors to ensure you meet standards.
Staying compliant protects your wallet and keeps your workplace safe.
Step 7: Invest in Technology
Technology makes inspections easier, faster, and more accurate. It’s worth considering if you manage a lot of assets.
Tech Tools to Try:
- Inspection Software: Apps let you create digital checklists, log findings, and track repairs.
- Mobile Devices: Use tablets or phones to record data on the go, with features like GPS stamps or photo uploads.
- Sensors: Install sensors to monitor things like temperature or vibration in real time, alerting you to issues.
- Drones: For hard-to-reach assets like roofs, drones can capture images or videos.
These tools save time and help you catch problems that might be missed in manual checks.
Common Mistakes to Avoid
Even with good intentions, people make mistakes that can lead to costly repairs. Here’s what to watch out for:
- Skipping Inspections: Missing even one check can let small issues grow into big ones.
- Ignoring Small Problems: A minor leak or loose bolt can cause major damage if ignored.
- Poor Training: Untrained inspectors might miss critical issues. Make sure your team knows what to look for.
- Bad Record-Keeping: Without clear logs, you can’t track trends or prove compliance.
- Cutting Corners: Rushing inspections or using cheap parts can lead to bigger problems later.
Avoiding these pitfalls ensures your inspections are effective and your assets stay in great shape.
The Payoff of Regular Inspections
Regular asset inspections are like insurance for your money and peace of mind. By catching issues early, you:
- Save Big on Repairs: Small fixes are way cheaper than replacing broken assets.
- Keep Things Running: Less downtime means more productivity and fewer headaches.
- Stay Safe: Fewer accidents protect your team and your reputation.
- Extend Asset Life: Well-maintained assets can last years longer, saving you replacement costs.
- Avoid Fines: Compliance keeps you out of legal trouble.
For example, regular roof inspections can save building owners thousands by catching leaks before they cause structural damage. The effort you put into inspections pays off in a big way.
Conclusion
Regular asset inspections are a smart way to protect your money, time, and safety. By knowing your assets, setting a schedule, using the right methods, acting on findings, maintaining between checks, staying compliant, and you can avoid expensive repairs and keep everything running smoothly. Asset Management 365 simplifies tracking, scheduling, and documenting inspections, ensuring your assets are always in top shape. Start today by listing your assets or scheduling your next inspection with Asset Management 365. Every step you take makes your assets last longer and your life easier. Don’t wait for a breakdown to act—get ahead of problems now.
Frequently Asked Questions
Why are regular asset inspections important?
They catch small problems before they become big, expensive repairs. Inspections also improve safety, ensure compliance with regulations, and extend the life of your assets, saving you money and downtime.
How often should I inspect my assets?
It depends on the asset. Daily checks are good for high-use equipment, while monthly or yearly inspections work for less-used items. Check manufacturer guidelines and consider how often the asset is used or exposed to harsh conditions.
What should I look for during an inspection?
Look for signs of wear, like cracks, leaks, or rust. Test functionality, like controls or brakes, and check safety features. Use checklists to make sure you cover everything.
Can I do inspections myself, or do I need a professional?
Simple visual checks can often be done yourself if you’re trained. For complex assets, like electrical systems or heavy machinery, hire certified inspectors to ensure accuracy and compliance.
How do I create an inspection checklist?
List key components of the asset, like engines or safety features, and what to check (e.g., leaks, noises). Include regulatory requirements and manufacturer recommendations. Software like FTQ360 can help you build custom checklists.
What happens if I skip inspections?
Skipping inspections increases the risk of breakdowns, safety hazards, and costly repairs. You might also face fines for not meeting regulations or lose warranties on your assets.