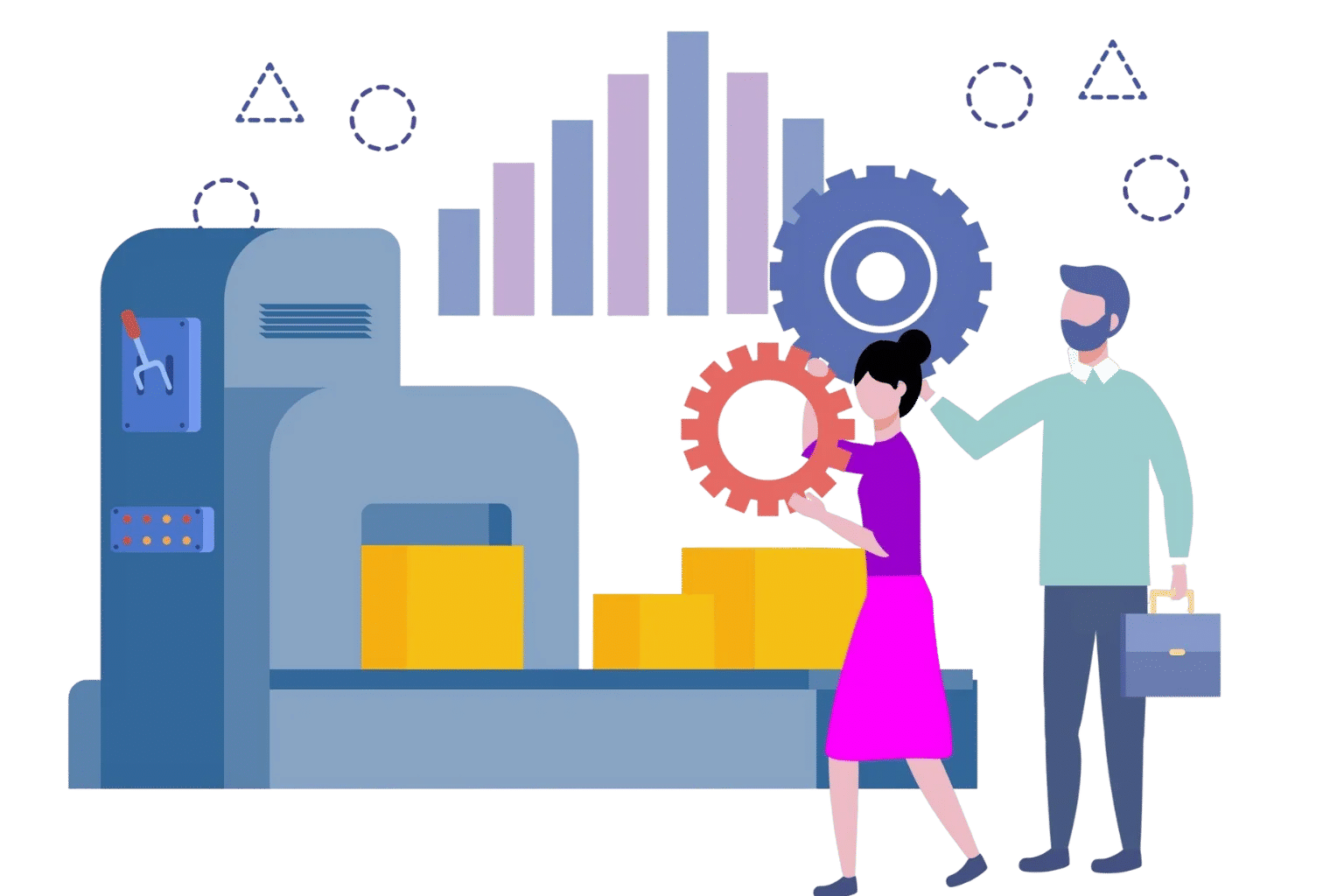
Asset Performance Management: A Key Strategy for Enhancing Equipment Longevity
In today’s fast-paced industrial landscape, maximizing the lifespan of equipment and assets is crucial for reducing costs and improving operational efficiency. While equipment failures are often inevitable, how you manage and maintain your assets can have a significant impact on their longevity.
✨
Quick Read
Summary generated by AI, reviewed for accuracy.
Asset Performance Management (APM) uses predictive maintenance and real-time monitoring to prevent equipment failures, reducing downtime and maintenance costs.
By leveraging data-driven insights, APM enhances asset reliability, improves efficiency, and extends the lifespan of equipment, providing long-term value.
One of the most effective strategies to achieve this is Asset Performance Management (APM). APM is a comprehensive approach to optimizing the performance and reliability of assets, helping organizations to improve the efficiency of their operations while extending the life of their equipment.
In this blog post, we’ll explore how Asset Performance Management can be a key strategy for enhancing equipment longevity. We’ll also discuss the fundamental aspects of APM, the various benefits it offers, and how to implement it in your organization.
What is Asset Performance Management?
Asset Performance Management (APM) refers to the use of strategies, technologies, and best practices to monitor and manage assets throughout their lifecycle. The goal of APM is to ensure that assets operate at peak performance, reduce the likelihood of unexpected failures, and extend their useful life. APM incorporates predictive maintenance, condition monitoring, and data analytics to enable organizations to make data-driven decisions about asset health and performance.
At its core, APM helps organizations shift from reactive maintenance practices—where problems are dealt with only after they occur—to a more proactive approach that aims to identify and address potential issues before they lead to costly repairs or unplanned downtime.
The Role of Predictive Maintenance in Enhancing Equipment Longevity
One of the central elements of Asset Performance Management is predictive maintenance. Predictive maintenance uses data collected from sensors and other monitoring technologies to predict when an asset is likely to fail or require maintenance. By leveraging techniques such as machine learning and advanced analytics, organizations can detect early warning signs of potential failures, allowing them to take corrective action before the problem escalates.
For example, vibration sensors on motors can detect irregularities in their performance, and temperature sensors on pumps can indicate whether they’re running outside of optimal parameters. These sensors provide continuous feedback about the condition of the equipment, which can be analyzed to predict when maintenance should be performed. This reduces the chances of catastrophic failures, ensuring that equipment remains operational for longer periods.
Condition Monitoring: Keeping Tabs on Asset Health
Condition monitoring is another critical component of Asset Performance Management. It involves regularly measuring the operational parameters of assets—such as pressure, temperature, and vibration—and comparing them to established benchmarks. By continuously tracking these parameters, you can identify early signs of wear or inefficiency that may indicate the need for maintenance or repairs.
Condition monitoring is especially valuable for critical equipment that operates in harsh or demanding environments, such as pumps, motors, compressors, and turbines. By staying ahead of potential issues, companies can plan maintenance activities more effectively and avoid unplanned downtime, leading to better equipment longevity and reduced operational disruptions.
Benefits of Asset Performance Management in Enhancing Equipment Longevity
Implementing an Asset Performance Management strategy comes with numerous benefits that directly contribute to equipment longevity:
1. Improved Reliability and Reduced Downtime
APM helps improve the reliability of assets by ensuring they are consistently performing within their optimal range. By detecting early signs of wear or malfunction, organizations can prevent sudden breakdowns, reducing unplanned downtime and the need for emergency repairs. The more reliable the equipment is, the longer it will last.
2. Prolonged Asset Lifespan
Regular monitoring and proactive maintenance activities enabled by APM help keep assets in peak operating condition. By identifying problems early, businesses can repair or replace parts before they fail completely, which prevents unnecessary wear and tear on equipment. This proactive approach extends the useful life of assets, enabling them to operate at optimal efficiency for a longer period.
3. Optimized Maintenance Schedules
With APM, organizations can shift from reactive to predictive maintenance. Instead of waiting for equipment to break down and react to failure, you can plan maintenance activities based on real-time data. This not only saves on repair costs but also ensures that equipment is maintained at the right intervals, reducing the risk of premature wear and tear.
4. Reduced Operational Costs
By enhancing equipment longevity and improving the efficiency of maintenance practices, APM reduces the cost of repairs and replacements. Predictive maintenance reduces the likelihood of catastrophic failures, which can be costly to repair. Moreover, optimized maintenance schedules and fewer instances of downtime contribute to overall cost savings.
5. Data-Driven Decision Making
APM integrates data from various sources such as sensors, historical maintenance records, and performance analytics to provide actionable insights. This data-driven approach allows managers to make informed decisions about asset health, replacement schedules, and capital investment. By analyzing performance trends over time, you can make smarter decisions about which assets need more attention and which can continue to operate efficiently.
Key Components of a Successful Asset Performance Management Strategy
To implement Asset Performance Management effectively, businesses need to incorporate several key components:
1. Advanced Sensor Technology
The backbone of APM is advanced sensor technology. Sensors that track variables such as temperature, vibration, and pressure provide real-time insights into asset performance. These sensors allow companies to monitor their assets continuously, identifying any anomalies or degradation in performance.
2. Data Analytics and Machine Learning
Data analytics plays a central role in Asset Performance Management. The vast amount of data generated by sensors needs to be processed and analyzed to uncover trends and patterns. Machine learning algorithms can identify potential issues and predict when assets may need maintenance, reducing the risk of failure. These predictive capabilities allow for more accurate maintenance planning and resource allocation.
3. Centralized Asset Management System
A centralized asset management system allows all asset-related data to be stored and accessed in one place. These systems offer dashboards that display asset performance metrics, maintenance schedules, and historical performance data. By having all information in one location, organizations can streamline their maintenance processes and improve their decision-making.
4. Skilled Workforce and Training
APM systems are only as effective as the team that operates them. For this reason, training and upskilling staff members is crucial to the success of your Asset Performance Management strategy. Operators, maintenance personnel, and engineers need to understand how to interpret data and respond to alerts from the APM system. Additionally, a skilled workforce can identify issues that the system may not be able to detect on its own.
5. Integration with Enterprise Systems
For APM to be fully effective, it must be integrated with other enterprise systems, such as Enterprise Resource Planning (ERP) and Computerized Maintenance Management Systems (CMMS). This integration allows for smoother coordination between asset monitoring, inventory management, and maintenance workflows, improving operational efficiency and asset management.
Challenges in Asset Performance Management
While Asset Performance Management offers many advantages, it is not without its challenges. Some of the most common issues include:
1. High Initial Costs
Implementing an APM system often requires significant upfront investment in sensor technology, software, and staff training. However, this cost is usually offset by the long-term savings resulting from fewer breakdowns, optimized maintenance, and extended asset lifespans.
2. Data Overload
With APM systems collecting vast amounts of data, it can be challenging to filter out the noise and focus on actionable insights. Companies must invest in robust data analytics tools that can process and interpret this data efficiently.
3. Integration Difficulties
Integrating APM systems with other enterprise systems can be complex, especially for organizations that rely on legacy equipment or older technologies. Successful integration requires a comprehensive approach to ensure that all systems are compatible and that data flows seamlessly between them.
Best Practices for Implementing Asset Performance Management
To successfully implement APM in your organization, consider the following best practices:
1. Start Small and Scale Gradually
Implementing APM can be overwhelming, especially for large organizations with numerous assets. Start with a pilot program for a specific set of assets and gradually scale up as you refine your processes.
2. Focus on Data Quality
Ensure that the data collected from sensors and monitoring systems is accurate and reliable. Poor data quality can lead to incorrect predictions and missed opportunities for maintenance.
3. Collaborate Across Teams
APM is a cross-departmental initiative that requires collaboration between operations, maintenance, and IT teams. Regular communication and alignment between these teams ensure that asset data is being used effectively to make informed decisions.
4. Monitor and Adjust Continuously
Once your APM system is in place, continuously monitor its performance and adjust your strategy as necessary. The key to success with APM is constant improvement and adaptation to new technologies and methods.
Conclusion
Asset Performance Management is a powerful strategy that can significantly enhance equipment longevity by enabling organizations to proactively monitor, maintain, and optimize their assets. By leveraging predictive maintenance, condition monitoring, and data analytics, businesses can prevent costly breakdowns, reduce downtime, and extend the useful life of their equipment. With careful implementation and a focus on data-driven decision-making, Asset Management 365 can help businesses improve operational efficiency, reduce costs, and increase the return on investment for their assets.
By adopting Asset Performance Management, you’re not just preserving equipment for the short term—you’re building a foundation for long-term success.
Join Our Creative Community
Frequently Asked Questions
How does Asset Performance Management improve equipment lifespan?
APM improves equipment lifespan by predicting potential failures before they occur, allowing organizations to perform maintenance or repairs proactively. This reduces wear and tear on equipment and helps avoid costly downtime, ultimately extending asset life.
What are the main components of Asset Performance Management?
The main components of APM include:
Predictive Maintenance: Anticipating when maintenance will be required based on data and analytics.
Condition Monitoring: Continuously monitoring the health of equipment through sensors and other tools.
Data Analytics: Using historical and real-time data to make informed decisions about asset management.
Asset Health Monitoring Systems: Systems designed to monitor the performance and condition of assets.
Maintenance Optimization: Streamlining maintenance schedules to ensure equipment operates at peak efficiency.
How does predictive maintenance contribute to APM?
Predictive maintenance plays a crucial role in APM by identifying potential problems before they become serious issues. By analyzing data from sensors and monitoring equipment, predictive maintenance allows organizations to address problems in advance, reducing downtime and repair costs.
What types of assets can benefit from Asset Performance Management?
A wide range of assets can benefit from APM, including:
Manufacturing equipment (motors, pumps, compressors)
Industrial machinery
Infrastructure assets (bridges, pipelines)
HVAC systems
IT infrastructure
Fleet management systems (vehicles, trucks)
Essentially, any asset with a defined lifecycle and maintenance needs can benefit from APM.
What is the ROI of Asset Performance Management?
The return on investment (ROI) from APM is substantial, with cost savings from reduced downtime, fewer emergency repairs, and extended asset life. APM also leads to more efficient use of resources and improved overall operational efficiency, resulting in greater profitability for businesses.
What challenges do organizations face when implementing APM?
Some common challenges in implementing APM include:
High initial setup costs for technology and infrastructure.
Difficulty integrating APM with existing systems (such as ERP or CMMS).
Managing large volumes of data and ensuring its accuracy.
Training employees to use APM tools effectively.
How do you implement Asset Performance Management in your organization?
To implement APM, start by:
Identifying critical assets that require monitoring.
Installing sensors and data collection tools to track asset performance.