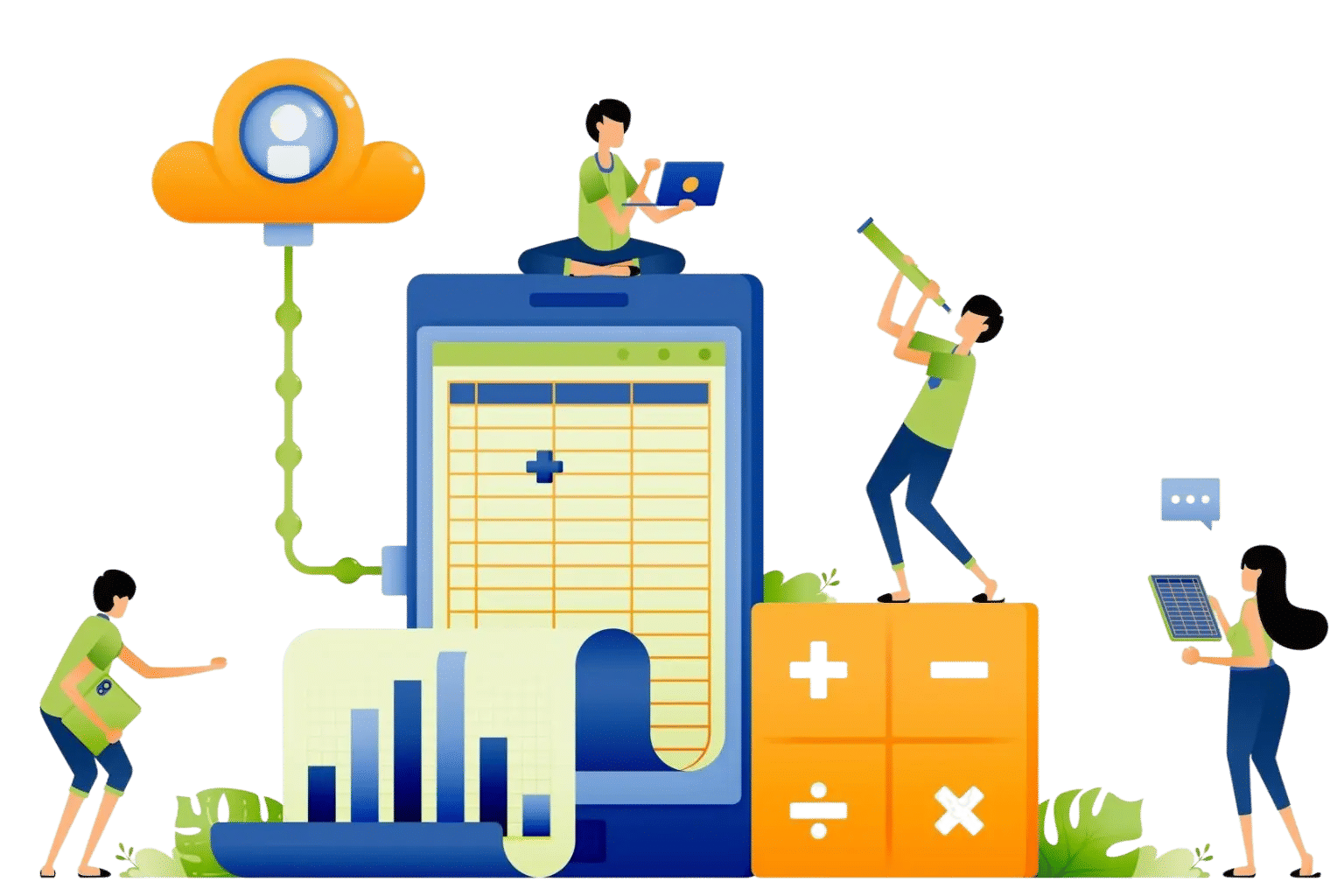
How to Simplify Maintenance Schedules with an Asset Management Inventory System
In any organization—whether in manufacturing, education, healthcare, or IT—keeping track of equipment health and maintenance timelines is not just good practice, it is essential. Missed maintenance can lead to unexpected breakdowns, costly repairs, and unplanned downtime. That is where an Asset Management Inventory System (AMIS) becomes an valuable tool. ent tools.
An asset management inventory system not only helps you track assets but also brings structure and automation to how you handle maintenance schedules. This article explains how businesses can simplify, automate, and enhance their maintenance schedules using modern asset managem
✨
Quick Read
Summary generated by AI, reviewed for accuracy.
An Asset Management Inventory System automates maintenance schedules by tracking asset details and sending timely reminders.
With real-time access and Microsoft 365 integration, teams reduce downtime and keep operations running smoothly.
What Is a Maintenance Schedule?
A maintenance schedule is a planned timeline that outlines when and how various assets (like machines, IT equipment, tools, or infrastructure) should be inspected, serviced, or repaired. These schedules can be:
- Preventive (scheduled to avoid breakdowns),
- Predictive (based on asset data trends), or
- Corrective (after an issue is identified).
Maintenance schedules typically include:
- Frequency of service (weekly, monthly, annually),
- Assigned personnel or teams,
- Expected downtime or service windows,
- Service checklists or SOPs.
Keeping this organized manually becomes increasingly difficult as a company grows. That is why a digital solution is necessary.
Why Maintenance Scheduling Is Critical for Businesses
Here is why having a maintenance schedule matters:
- Reduces Downtime: Regular maintenance prevents unexpected failures.
- Extends Asset Life: Timely care prolongs the working life of equipment.
- Improves Safety: Well-maintained equipment reduces the risk of workplace accidents.
- Ensures Compliance: Many industries are required by law to maintain equipment logs.
- Saves Money: Proactive maintenance is more cost-effective than emergency repairs.
A well-executed schedule helps businesses move from reactive to proactive operations.
Challenges in Traditional Maintenance Scheduling
Without an asset management system, organizations often struggle with:
- Manual Spreadsheets: Easily outdated, hard to maintain, and prone to human error.
- Lack of Alerts: No automated reminders or warnings.
- Inconsistent Records: Service logs and history are scattered or incomplete.
- Resource Conflicts: Scheduling overlaps or assigning unavailable technicians.
- Missed Maintenance Windows: No real-time visibility into what is due or overdue.
All of these challenges can negatively affect productivity and compliance.
What Is an Asset Management Inventory System?
An Asset Management Inventory System (AMIS) is a software solution designed to help organizations track, manage, and maintain their physical and digital assets throughout their lifecycle — from acquisition to disposal.
This system goes beyond simple inventory tracking. It ensures every asset is accounted for, maintained on schedule, and utilized efficiently.
Here is what it typically includes:
Asset Identification & Tagging: Assigns unique IDs using barcodes, QR codes, or RFID for easy tracking.
Inventory Tracking: Monitors the location, quantity, and status of each asset in real-time.
Maintenance Scheduling: Automates service alerts and logs service history to improve asset longevity.
Lifecycle Management: Tracks purchase, depreciation, usage, and retirement of assets.
User Assignment & Access Control: Records which team or individual is using the asset, with role-based permissions.
Reporting & Analytics: Provides insights into usage, cost, performance, and audit trails.
Whether you are managing IT equipment, machinery, office supplies, or infrastructure, an AMIS ensures that nothing slips through the cracks. It brings structure, accountability, and efficiency — saving time and reducing costs for organizations of all sizes.
How Asset Management Helps in Maintenance Scheduling
An Asset Management Inventory System (AMIS) plays a vital role in simplifying and optimizing maintenance scheduling. It shifts businesses from reactive fixes to proactive planning.
Here is how asset management supports efficient maintenance:
Centralized Maintenance Records
All asset details — including maintenance history, service contracts, and usage data — are stored in one place, making it easy to track and plan.
Automated Maintenance Alerts
You can set time-based or usage-based alerts, so the system notifies your team when a service is due, preventing missed schedules.
Custom Maintenance Plans
Different assets require different care. AMIS allows you to create tailored service routines based on asset type, usage, or condition.
Technician Assignment & Work Orders
Assign tasks directly through the system and track work order completion, ensuring accountability and timely execution.
Service Logs & Performance Data
Track repairs, inspections, and part replacements over time, helping teams refine future schedules and make informed decisions.
Reduced Downtime
Scheduled maintenance reduces the chance of unexpected failures, keeping operations running smoothly.
In short, asset management transforms maintenance into a structured, automated process that saves time, lowers costs, and increases asset reliability.
Key Features That Simplify Maintenance with AMIS
Identify Your Asset Data Sources
A well-designed Asset Management Inventory System (AMIS) streamlines maintenance by offering smart features that automate tasks, reduce errors, and improve efficiency. Below are the core features that make maintenance simpler:
Centralized Asset Database
All assets are listed with complete details—location, usage history, warranty, and service logs—making tracking and maintenance planning easier.
Automated Reminders & Alerts
The system sends automatic alerts for upcoming maintenance tasks, overdue services, or expiring warranties, helping you stay proactive.
Customizable Maintenance Schedules
You can define service frequency based on time, usage, or asset condition, ensuring each asset gets the attention it needs.
Digital Work Orders & Task Assignment
Generate work orders with detailed instructions and assign them to technicians. Track task status in real-time.
Mobile Access for Field Teams
Technicians can access schedules, update logs, and close tasks on the go—no need for paperwork or back-office updates.
Maintenance History & Audit Trail
Every action is recorded for future reference and compliance, making audits stress-free and data-driven.
These features help businesses move from reactive fixes to proactive planning—saving time, cost, and resources.
Benefits of Using AMIS for Maintenance
Implementing an Asset Management Inventory System (AMIS) offers practical benefits that go beyond asset tracking. It transforms how organizations manage maintenance operations:
Reduces Downtime
Automated scheduling and alerts help prevent unexpected equipment failures by ensuring timely servicing.
Enhances Asset Life
Regular maintenance extends the lifespan of machinery, tools, and IT assets, reducing replacement costs.
Improves Team Productivity
Technicians have clear task assignments, mobile access to checklists, and real-time updates, minimizing delays.
Supports Compliance & Audits
Maintenance logs and digital records make it easier to meet industry standards and pass inspections.
Saves Time & Costs
Eliminates manual tracking, reduces emergency repairs, and enables better resource planning.
Increases Visibility
Dashboards and reports offer full visibility into asset performance, service history, and pending tasks.
AMIS turns maintenance from a reactive task into a proactive, strategic advantage.
How to Implement Maintenance Scheduling in AMIS
Setting up maintenance scheduling in an Asset Management Inventory System (AMIS) is simple when done methodically. Here is how you can get started:
Identify and Register Assets
Add all serviceable assets into the system with key details like model, location, purchase date, and warranty.
Define Maintenance Schedules
Set time-based (e.g., monthly) or usage-based (e.g., after 100 hours of operation) schedules for each asset category.
Enable Alerts and Notifications
Configure automated reminders for upcoming services, overdue tasks, or inspection deadlines.
Assign Technicians or Teams
Allocate responsibilities to the right personnel to avoid delays or confusion.
Digitize Work Orders
Create and track work orders within the system, including checklists and documentation.
Monitor and Improve
Use reports to analyze maintenance trends, costs, and performance for continuous improvement.
This structured approach ensures efficient, error-free scheduling and better asset reliability.
Best Practices for Maintenance Scheduling
Start with Critical Assets
Prioritize high-value or high-risk equipment to minimize disruption.
Use Data to Set Schedules
Base maintenance on usage trends, not just time intervals.
Standardize Checklists
Create consistent procedures for each asset type to avoid missed steps.
Train Your Team
Ensure technicians understand the system, schedules, and responsibilities.
Review and Adjust Regularly
Analyze performance and downtime reports to refine schedules.
Integrate with Other Tools
Connect maintenance with helpdesk or procurement systems for smoother workflows.
Following these practices ensures reliable operations and longer asset life.
Common Mistakes to Avoid
Skipping Asset Registration: Failing to log all assets leads to incomplete maintenance coverage.
Relying Only on Time-Based Schedules: Ignoring usage data can result in over- or under-servicing assets.
Neglecting Overdue Tasks: Letting tasks pile up disrupts schedules and increases breakdown risk.
Lack of Team Training: Untrained staff may misuse the system or miss critical steps.
No Review or Optimization: Not analyzing maintenance logs prevents process improvement.
Missing Alerts: Overlooking automated reminders leads to missed service deadlines.
Avoiding these errors keeps your maintenance process efficient and reliable.
Conclusion
Keeping track of maintenance schedules does not have to be a manual nightmare. With an Asset Management 365, organizations can automate reminders, assign tasks, monitor performance, and protect asset health—all from a centralized platform.
Whether you are managing IT assets, medical equipment, or field tools, using a digital asset inventory system saves time, reduces costs, and builds a stronger maintenance culture.
Join Our Creative Community
Frequently Asked Questions
Can small businesses use AMIS for maintenance?
Yes, even small teams benefit from simplified scheduling, especially if they manage multiple assets across departments.
Does an AMIS need to be cloud-based?
While not mandatory, cloud-based systems offer better accessibility, automatic backups, and lower IT maintenance costs.
What kinds of alerts can be automated?
You can automate alerts for upcoming maintenance, overdue tasks, expiring warranties, and usage-based triggers.
Can I track service vendors through AMIS?
Yes, most systems allow vendor assignments and record of external work orders and service reports.
How long does it take to set up a maintenance schedule in AMIS?
For a small business, setup can be done in a few hours. Larger organizations might need a few days depending on the asset volume and complexity.