Onboarding Solutions for Manufacturing Companies
Onboarding solutions for manufacturing companies automate training, compliance, and document management, reducing errors and boosting efficiency from day one.
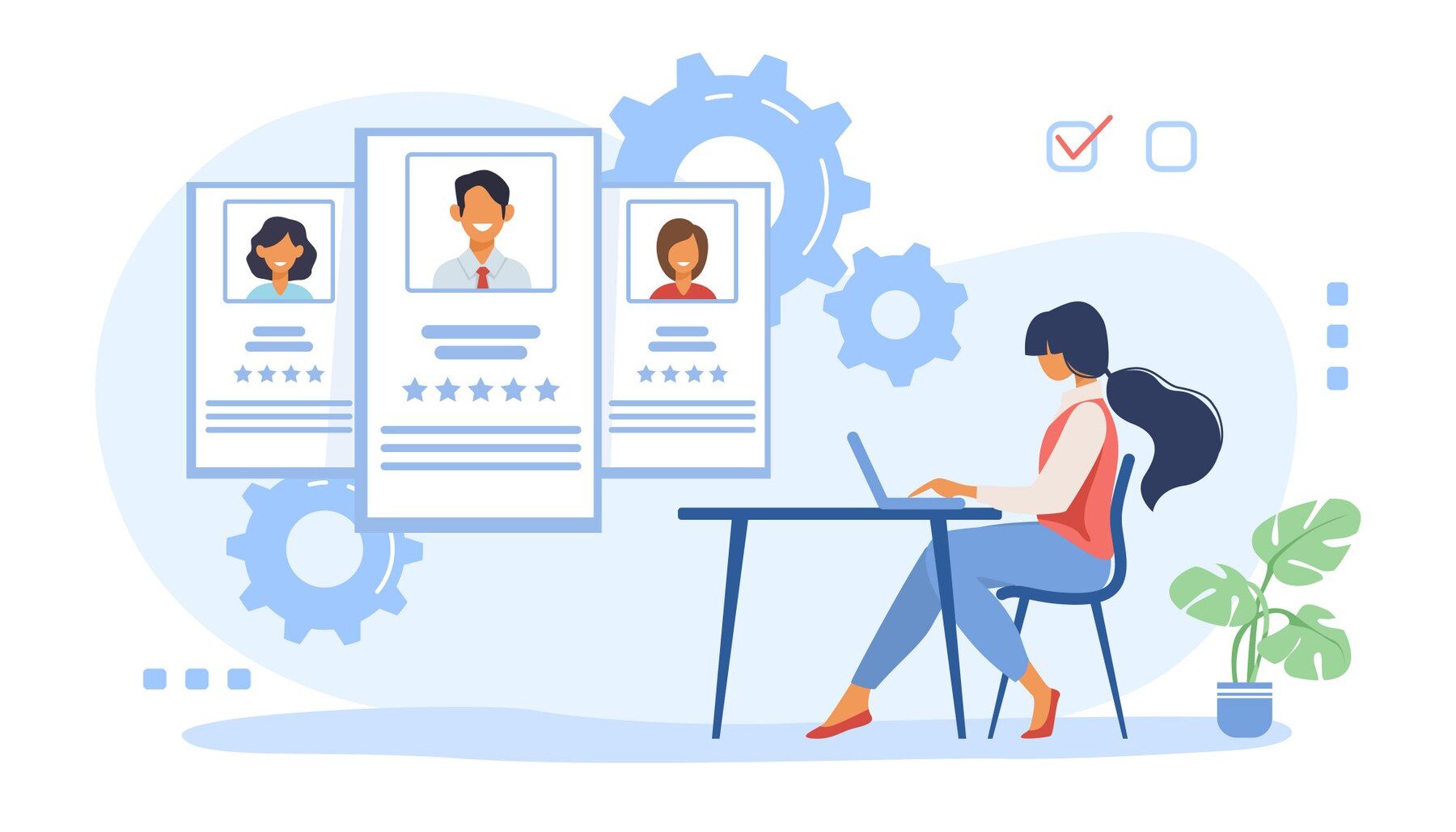
Are you ready to make onboarding a breeze for your new employees? Whether you’re running a small manufacturing facility or managing a large-scale plant, Employee Onboarding is designed to simplify your employee integration process.Say goodbye to paperwork headaches and long hours of manual work EO offers a solution that saves time, boosts compliance, and ensures your new hires are up to speed in no time.
Why Does Onboarding Matter in Manufacturing?
In the fast-paced world of manufacturing, time is money. Onboarding is more than just a “welcome” session it is about equipping your new employees with the right tools, training, and compliance knowledge to succeed on the job. A structured performance management system helps integrate workers faster, ensures safety, and aligns new hires with company goals.
Studies show that companies with robust onboarding systems see a 30% boost in productivity , while improving employee retention and engagement. And let’s face it who does not want to reduce turnover and have more time for high-value tasks?
The Challenges of Traditional Onboarding in Manufacturing
Onboarding in manufacturing can be a complex and time-consuming process, often marked by challenges that slow down productivity and compliance. While traditional onboarding methods might have worked in the past, they can no longer keep up with the fast-paced demands of modern manufacturing environments. Let’s take a closer look at the key challenges of traditional onboarding and how they impact both new hires and the organization.
1. Manual Paperwork and Documentation
One of the most significant challenges in traditional onboarding is the overwhelming amount of paperwork. New employees are often required to fill out forms, sign documents, and submit certifications—all of which can be prone to errors or delays. This manual process not only takes time but also increases the risk of missing important documents, leading to compliance issues. The burden of paperwork often results in unnecessary delays in getting employees up to speed, which directly affects productivity.
2. Inefficient Training Processes
Training in manufacturing is crucial, especially when it comes to safety standards, equipment handling, and regulatory compliance. However, traditional onboarding often relies on in-person sessions or paper-based manuals, which can be inconsistent and difficult to track. Employees may not be able to access training materials on-demand, or they might forget key lessons if they don’t have ongoing support. This disjointed approach to training can result in knowledge gaps, slower integration, and potentially higher risk of accidents or mistakes on the shop floor.
3. Lack of Standardization
In traditional onboarding, the process can vary significantly between departments or even from one manager to another. Without a standardized approach, new hires may receive inconsistent information, and different teams might have different expectations for their roles. This lack of uniformity leads to confusion, misalignment, and can even affect the company culture, as new employees are not introduced to the same values and expectations across the board.
4. Difficulty in Tracking Progress
With traditional onboarding methods, it’s challenging to monitor the progress of new hires in real-time. Managers often rely on verbal check-ins or paper tracking systems to assess how well employees are progressing through their training. This can result in missed opportunities to provide timely feedback or support when needed. Without the ability to track progress efficiently, some new hires may fall behind, while others may feel underutilized or unsupported.
5. Compliance and Safety Risks
In manufacturing, staying compliant with industry standards and ensuring safety are paramount. Traditional onboarding processes often rely on in-person safety training sessions, which can be difficult to schedule and track. As a result, employees may not complete training on time, putting the company at risk of non-compliance. Additionally, inconsistent safety training can lead to accidents or injuries on the job, further compounding the issue.
From Assembly Line to Excellence: Optimizing Onboarding for Manufacturing Success
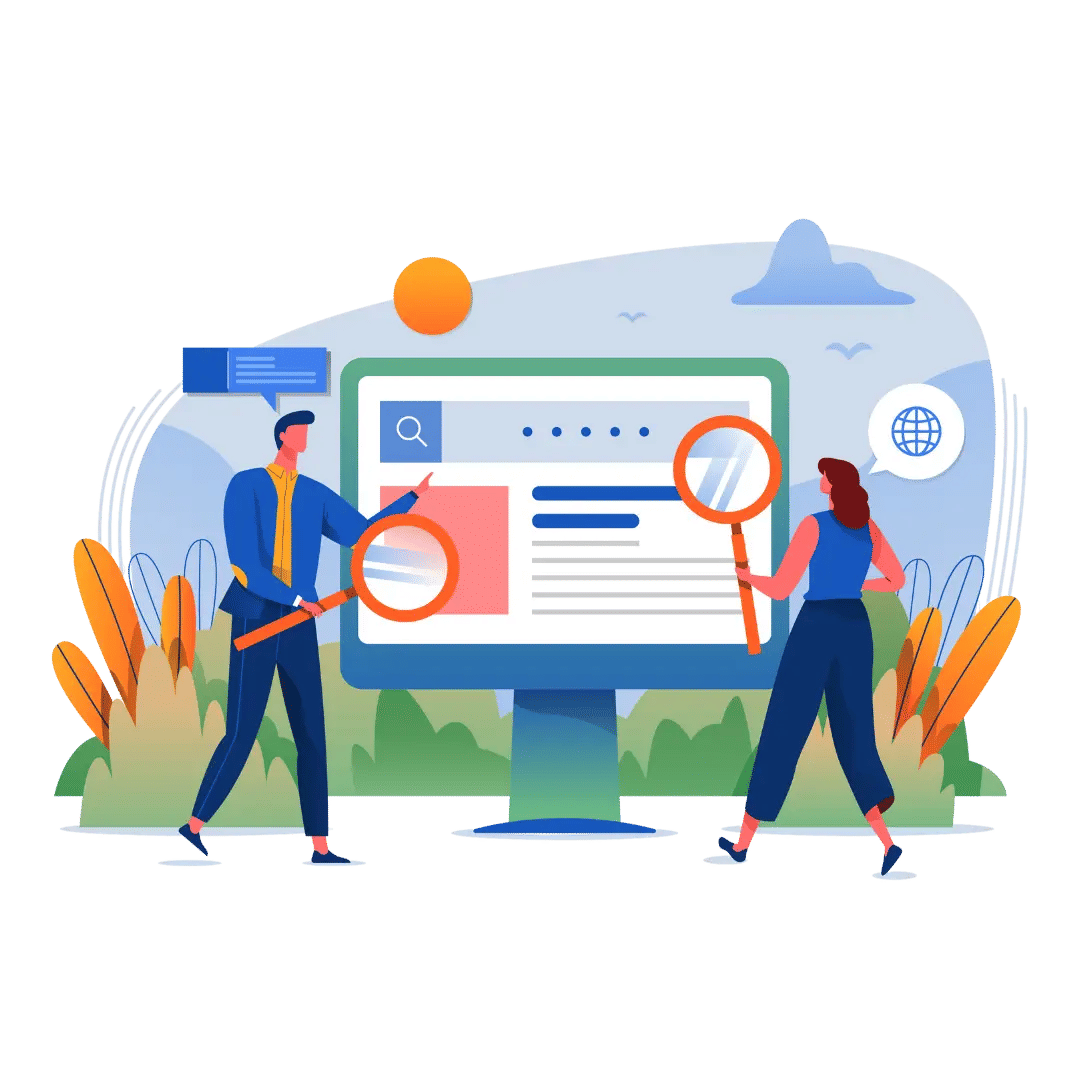
Get Started with SMART Goals: Setting Your Team Up for Success
Before diving into onboarding, it’s crucial to set SMART goals. These goals provide a clear direction and ensure your new hires stay focused and motivated. Here’s how to set them up for success:
- Specific: Define clear, measurable targets. Instead of “increase sales,” say “increase production by 10% in the next quarter.” Specific goals remove ambiguity and help your team understand exactly what is expected of them.
- Measurable: Track progress with key performance indicators (KPIs), like training completion rates or safety compliance, to ensure goals are on track. Measurability allows you to monitor progress in real-time and adjust where necessary.
- Achievable: Set realistic yet challenging goals. For example, reducing downtime by 5% within a quarter is attainable and motivating. Setting achievable targets ensures your team is engaged without overwhelming them.
- Relevant: Align goals with company objectives, such as improving safety or increasing production efficiency, to contribute to overall success. When goals are relevant, they directly support both team growth and business priorities.
- Time-bound: Create deadlines to keep progress on track. For example, “Complete onboarding training in 30 days” ensures focus and timely completion. A clear timeline keeps the team focused and makes the process more efficient.
By setting SMART goals, you provide your team with a clear roadmap for success, ensuring they stay motivated and aligned with company objectives. This helps drive both individual and company-wide growth from day one. SMART goals act as a motivational tool, guiding new hires while reinforcing a sense of accomplishment as they meet each milestone.
Why EO is the Perfect Fit for Manufacturing Companies
EO is not just another onboarding software it is specifically designed to address the unique challenges that manufacturing companies face, from compliance to training to high turnover rates.
Key Features of EO:
- Seamless Safety Training
Compliance with safety regulations is non-negotiable in manufacturing. EO offers customizable safety training modules that employees can complete anytime, anywhere ensuring they are equipped for the job before they even step onto the floor. - Automated Document Management
Say goodbye to chasing down forms and signatures. EO automates the document collection and ensures all compliance requirements are met before the new hire starts working. With EO, all documents are stored securely and can be accessed at any time. - Scalable for Any Size Team
Whether you are onboarding 10 or 500 new hires, EO scales with your business. From small factories to large enterprises, EO’s platform adapts to your team’s size and needs. - Real-Time Tracking & Updates
Monitor the progress of your employees with real-time tracking, ensuring all tasks training, paperwork, and certifications are completed on time. Immediate updates also help you stay proactive about any potential delays.
How Onboarding Reduces Onboarding Time and Increases Productivity
Effective onboarding sets the foundation for employee success and productivity. For manufacturing companies, a streamlined onboarding process significantly reduces the time it takes for new hires to become productive contributors. Here’s how a well-executed onboarding solution can achieve both.
1. Streamlined Training and Certification
Traditional training methods involve lengthy in-person sessions and paperwork. With automated onboarding solutions, like EO, training modules are delivered digitally, enabling new hires to complete them at their convenience. Real-time tracking ensures training is completed efficiently, reducing downtime and accelerating the integration process.
2. Automated Documentation and Compliance
Manually collecting and processing paperwork is time-consuming. Onboarding software automates this by verifying and storing all necessary documentation electronically. This reduces administrative tasks, minimizes errors, and accelerates the process of getting new hires on the floor faster.
3. Standardized Onboarding Experience
A consistent onboarding experience ensures that all new hires receive the same training and support. A centralized onboarding platform helps monitor progress, eliminates knowledge gaps, and leads to smoother integration into roles, improving performance from day one.
4. Faster Access to Tools and Resources
New hires can access the tools, resources, and information they need immediately, instead of waiting for assignments. Onboarding platforms provide quick access to materials, allowing employees to begin contributing right away and increasing productivity.
5. Real-Time Monitoring and Feedback
Onboarding solutions provide real-time tracking, allowing managers to monitor progress and offer timely feedback. This ensures that any necessary adjustments are made quickly, helping new hires become productive sooner.
6. Employee Engagement and Motivation
A well-designed onboarding process creates a positive first impression, enhancing employee engagement. When new hires feel supported and prepared, they are more motivated and productive, reducing turnover and improving long-term performance.
How EO Benefits Manufacturing Companies
Faster Onboarding: Reduce your onboarding time by automating training, document collection, and compliance checks. This streamlined process ensures your new hires can quickly get up to speed and start contributing to your business right away.
Boosted Compliance: Keep your team on track with real-time updates and automated reminders for training and certification deadlines. With EO, you will never miss a compliance requirement again, ensuring your workforce is always prepared and legally compliant.
Increased Productivity: Onboard new employees faster, allowing them to become productive contributors to the team sooner. The sooner they are trained, the faster they can help drive your business forward, increasing overall team efficiency.
Improved Retention: A streamlined and engaging onboarding process keeps your employees satisfied and reduces turnover. By providing a seamless and supportive experience, EO helps your team feel more connected and committed to your company’s success.
EO in Action: Real Manufacturing Success Stories
Still wondering how EO works in real-life scenarios? Here’s an example:
XYZ Manufacturing, a global manufacturing leader, reduced onboarding time by 50% and improved safety compliance by 30% after integrating EO’s automated training and document management system. This allowed the company to onboard new hires quickly, boosting productivity and ensuring all new employees met safety standards before their first shift.
EO’s automated document collection ensured all compliance requirements were met and stored securely in real-time, eliminating paperwork delays. As a result, XYZ Manufacturing reduced safety risks and enhanced team confidence, leading to lower turnover rates and a more productive, compliant workforce.
Want to see how EO can streamline your onboarding? Schedule a demo today!
The Benefits of EO for Manufacturing Companies
Not only does EO save time, but it also improves the employee experience from day one. By streamlining onboarding processes, EO helps you get new hires up to speed faster and ensures that your manufacturing team is always compliant, safe, and productive. Here’s how EO can benefit your business:
- Faster Training and Integration
Get your new employees trained, certified, and productive quickly, reducing downtime and speeding up the process of getting them on the shop floor. With EO’s intuitive training modules and automated systems, employees can immediately begin the learning process and engage in hands-on tasks sooner, leading to quicker integration into their roles. - Enhanced Safety and Compliance
Safety training is more critical than ever in manufacturing, and EO ensures that all your employees meet safety standards right from the start. With customizable safety modules, automated tracking, and real-time compliance updates, you ensure your workforce is always up-to-date with the latest regulations. By proactively addressing safety and compliance needs, EO helps reduce risks and liability. - Automated Document Management
Say goodbye to chasing down signatures or filling out the same forms repeatedly. EO automates all paperwork, saving time and preventing errors. With automated document collection, secure storage, and real-time tracking of all necessary compliance forms, you’ll never worry about missing paperwork or delayed approvals. - Streamlined Communication and Collaboration
EO enhances communication within your team by providing a centralized platform where all new hire documents, training records, and feedback are stored and easily accessible. This collaborative approach ensures that managers, HR teams, and employees are on the same page throughout the onboarding process. - Ready to Revolutionize Your Onboarding Process?
It is time to take the guesswork out of onboarding. EO helps you onboard new hires faster, with greater compliance and efficiency leading to a more productive, engaged workforce.
Schedule a demo today and see how EO can streamline your onboarding process!
Conclusion
In today’s fast-paced manufacturing environment, time is of the essence. Employee Onboarding 365 helps you ensure that new hires are up to speed quickly, safely, and effectively. With automated features, real-time tracking, and compliance-focused tools, EO is designed to meet the unique needs of the manufacturing industry.
By choosing EO, you are investing in a smooth, efficient onboarding process that not only saves time but also ensures your employees feel valued and supported from day one. Start transforming your employee onboarding experience with EO today!
Empower Your Workforce
Revolutionize your manufacturing onboarding with solutions that enhance efficiency, safety, and compliance from day one
Frequently Asked Questions
How does Employee onboarding help with safety training compliance?
EO offers customizable safety training that’s accessible to employees anytime. All training modules are compliant with industry regulations, ensuring that your workforce is fully trained and safe from day one.
Can EO accommodate large manufacturing teams?
Yes, EO is fully scalable and can handle onboarding for teams of any size, whether you’re managing hundreds or thousands of employees across multiple locations.
Is EO easy to integrate with other systems?
EO integrates seamlessly with most HR and payroll systems, allowing you to synchronize data without the hassle of manual entry.
How can onboarding solutions improve employee retention?
EO’s engaging onboarding process fosters a positive first impression, improving employee satisfaction and retention. By ensuring smooth integration and a focus on continuous learning, new employees feel valued and supported.
What kind of support does EO provide?
EO offers full support, from training resources to a dedicated customer service team. Our platform is designed to make onboarding easy, but we’re here to help if you need assistance.