Why Onboarding for Manufacturing Matters More Than You Think
Onboarding in manufacturing helps new hires adapt quickly to safety protocols and productivity standards, boosting retention and efficiency.
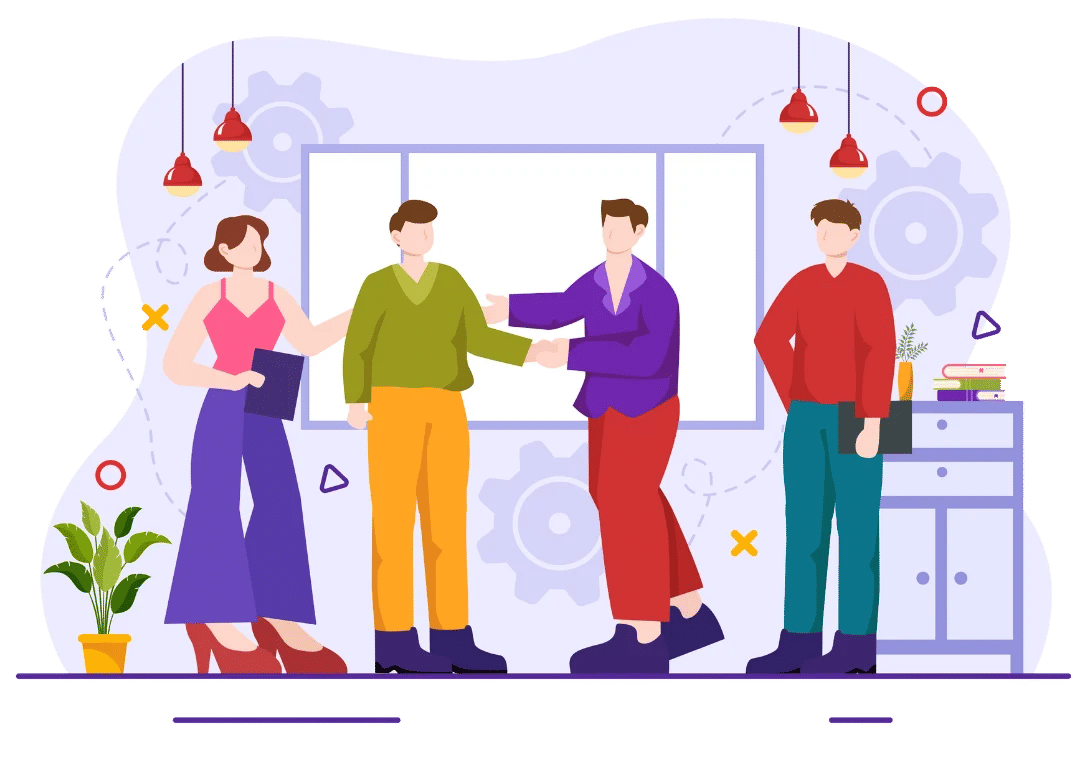
Starting a new job can be overwhelming, especially in manufacturing, where processes are complex, and safety is critical. A well-planned onboarding program helps new hires feel confident, stay safe, and become productive faster.
The Importance of Onboarding for Manufacturing
Onboarding for manufacturing goes beyond paperwork it ensures precision, safety, and efficiency. A structured program helps new hires quickly adapt to machinery, regulations, and productivity standards, reducing risks and turnover.
Effective onboarding boosts confidence, engagement, and job readiness, leading to a safer, more productive workforce.
1. Enhancing Workplace Safety
Manufacturing HR Onboarding Software involves heavy machinery, hazardous materials, and complex processes. Proper onboarding ensures that employees:
- Receive comprehensive safety training on equipment operation, protective gear usage, and emergency response.
- Understand regulations and other industry-specific safety standards.
- Learn how to identify and report workplace hazards to prevent accidents.
- Participate in hands-on training and safety drills to reinforce best practices.
2. Increasing Productivity and Efficiency
A structured onboarding process equips employees with the skills and knowledge needed to perform their roles effectively. This includes:
- Providing clear job descriptions and performance expectations.
- Offering step-by-step training on production processes and quality control.
- Assigning mentors or experienced workers to guide new hires.
- Using technology-driven learning tools like virtual reality (VR) simulations or interactive training modules.
3. Reducing Employee Turnover
High turnover is a common challenge in manufacturing, often due to a lack of support during the early stages of employment. Effective onboarding for manufacturing helps retain employees by:
- Creating a welcoming and inclusive environment to foster a sense of belonging.
- Ensuring new hires understand their career growth opportunities within the company.
- Addressing concerns and providing regular feedback and check-ins during the initial months.
- Encouraging team-building activities to build strong workplace relationships.
4. Ensuring Compliance and Standardization
Manufacturing Onboarding Software companies must comply with various industry regulations and internal policies. A well-structured onboarding software solution for manufacturing employees.
- Ensures employees understand compliance requirements from day one.
- Reduces legal risks by providing clear documentation of company policies and procedures.
- Standardizes training across all departments, ensuring consistency in work quality and safety practices.
- Helps avoid costly errors and regulatory fines by emphasizing compliance with safety and operational protocols.
5. Improving Employee Engagement and Job Satisfaction
When employees feel valued and well-prepared for their roles, they are more likely to stay engaged and motivated. Onboarding Software in Manufacturing enhances engagement by:
- Introducing employees to the company’s mission, values, and culture.
- Providing opportunities for open communication with leadership.
- Encouraging a collaborative and supportive work environment.
- Recognizing and celebrating early achievements and milestones.
Why Effective Onboarding Matters
- Reduces Turnover: Manufacturing hr onboarding software has a high turnover rate. A structured onboarding program helps new employees feel valued and engaged, increasing retention.
- Improves Safety: Proper training reduces workplace accidents by ensuring employees understand safety protocols from day one.
- Boosts Productivity: Employees who receive clear instructions and hands-on training perform better and adapt quickly.
- Enhances Job Satisfaction: When workers feel prepared and supported, they are more likely to stay and contribute positively.
- Ensures Compliance: Manufacturing involves strict industry regulations. Onboarding ensures that employees follow the necessary guidelines.
Key Steps for Onboarding for Manufacturing Workers
A structured onboarding for manufacturing process makes a huge difference in setting new hires up for success. Here are the key steps:
1. Pre-Boarding: Set the Stage
Before the employee’s first day, send them essential information to ensure they are well-prepared and confident. This includes:
- Job expectations and responsibilities: Provide a clear outline of daily tasks, performance expectations, and key objectives so employees understand their role before they start.
- Safety manuals and compliance guidelines: Ensure they are aware of workplace safety policies, emergency protocols, and industry regulations to maintain a safe work environment.
- Facility maps and dress code policies: Help them navigate the workplace by sharing maps, parking information, and dress code requirements to ensure they come prepared on day one.
- Required forms and documentation: Send tax forms, employment agreements, and any other paperwork in advance to avoid delays and unnecessary stress on their first day.
By handling these details early, new hires can focus on learning and integrating into their role more smoothly.
2. Day One: Welcome and Orientation
The first day should be a welcoming and informative experience that sets a positive tone. Key elements include:
- A warm introduction to the team and management: Arrange a meet-and-greet session where new hires can connect with colleagues, supervisors, and key stakeholders to build relationships.
- A facility tours to familiarize them with work areas, exits, and restrooms: Walk them through different sections of the workplace, including break rooms, production areas, emergency exits, and first-aid stations.
- Basic safety training and emergency procedures: Conduct an overview of emergency exits, fire drills, first-aid locations, and workplace safety policies to ensure awareness from day one.
- Setting up workstations, ID badges, and login credentials: Ensure that computers, access cards, lockers, and necessary tools are ready to minimize downtime and allow them to start work efficiently.
A well-structured first day leaves a lasting impression and helps new employees feel valued and comfortable.
3. Safety Training: A Non-Negotiable Step
Workplace safety is a top priority, especially in manufacturing hr software onboarding. Onboarding must include comprehensive safety training, covering:
- Proper handling of tools and machinery: Demonstrate the correct usage of equipment, including common mistakes to avoid, maintenance tips, and safety mechanisms.
- Personal Protective Equipment (PPE) usage: Explain the importance of wearing PPE, how to properly fit and maintain it, and when it is required for specific tasks.
- Emergency response protocols: Train employees on fire drills, spill containment, medical emergencies, and how to report incidents quickly and correctly.
- Hazard communication and risk prevention: Educate workers on recognizing potential hazards, reading safety labels, and following standard operating procedures to prevent workplace accidents.
Using hands-on demonstrations, real-world scenarios, and interactive training helps reinforce safety protocols effectively.
4. Job-Specific Training
Each role requires specialized skills, so training should be tailored to help employees succeed in their specific position. This includes:
- Step-by-step guidance on job tasks: Provide clear, written instructions and demonstrations on daily responsibilities to ensure clarity and efficiency.
- Shadowing experienced workers for real-time learning: Allow new hires to observe skilled workers performing tasks, asking questions, and learning best practices directly from experienced colleagues.
- Practice sessions with feedback to improve skills: Give employees opportunities to practice their tasks under supervision and receive constructive feedback to refine their techniques.
Gradual, structured training ensures employees feel comfortable and confident in their roles, leading to higher job performance.
5. Assign a Mentor or Buddy
Pairing new employees with experienced team members helps them adjust faster and feel supported. A mentor or buddy can:
- Answer questions and provide guidance: Having a go-to person for workplace-related questions ensures new hires don’t feel lost or overwhelmed.
- Share best practices and tips: Experienced employees can provide insights on efficiency, teamwork, and problem-solving strategies that aren’t always covered in formal training.
- Offer support and encouragement: Starting a new job can be stressful, but having someone to rely on for support helps build confidence and reduces frustration.
A mentor system fosters a sense of belonging and enhances employee engagement from the start.
6. Set Clear Performance Expectations
New hires need a clear understanding of what success looks like in their role. Set expectations through:
- Measurable goals and key performance indicators (KPIs): Define specific performance targets, such as productivity levels, quality standards, and efficiency benchmarks.
- Regular feedback sessions to track progress: Schedule weekly or monthly check-ins to discuss strengths, areas for improvement, and any challenges they may be facing.
- Encouragement and support for improvement: Offer constructive feedback and additional training if needed, ensuring employees feel motivated and capable of meeting expectations.
Setting clear performance standards reduces uncertainty and keeps employees aligned with company goals.
7. Ongoing Training and Development
Onboarding for manufacturing shouldn’t end after the first few days. Continuous learning is crucial for long-term growth and job satisfaction. Provide opportunities such as:
- Advanced skills training sessions: Offer workshops, technical training, or cross-training in other departments to expand employees’ knowledge and versatility.
- Leadership development programs: Identify potential future leaders and provide management training to help them advance within the company.
- Opportunities for certifications and promotions: Support employees in obtaining industry certifications, skill-based credentials, and career progression within the organization.
Ongoing development helps retain top talent and keeps employees engaged in their roles.
8. Gather Feedback and Improve the Process
To refine and enhance the onboarding experience, regularly collect feedback from new hires. This can be done through:
- Employee surveys and one-on-one meetings: Ask new hires about their experience, what worked well, and what could be improved in the onboarding process.
- Identifying gaps in training and onboarding materials: Review feedback to see if any critical information is missing or if additional resources are needed.
- Making continuous improvements to the onboarding process: Use insights gained from feedback to make necessary adjustments, ensuring a smoother experience for future hires.
An adaptable onboarding process leads to higher satisfaction, better retention, and a more effective workforce.
Streamline your entire employee onboarding process from hiring to integration, all in one centralized platform with EO 365.
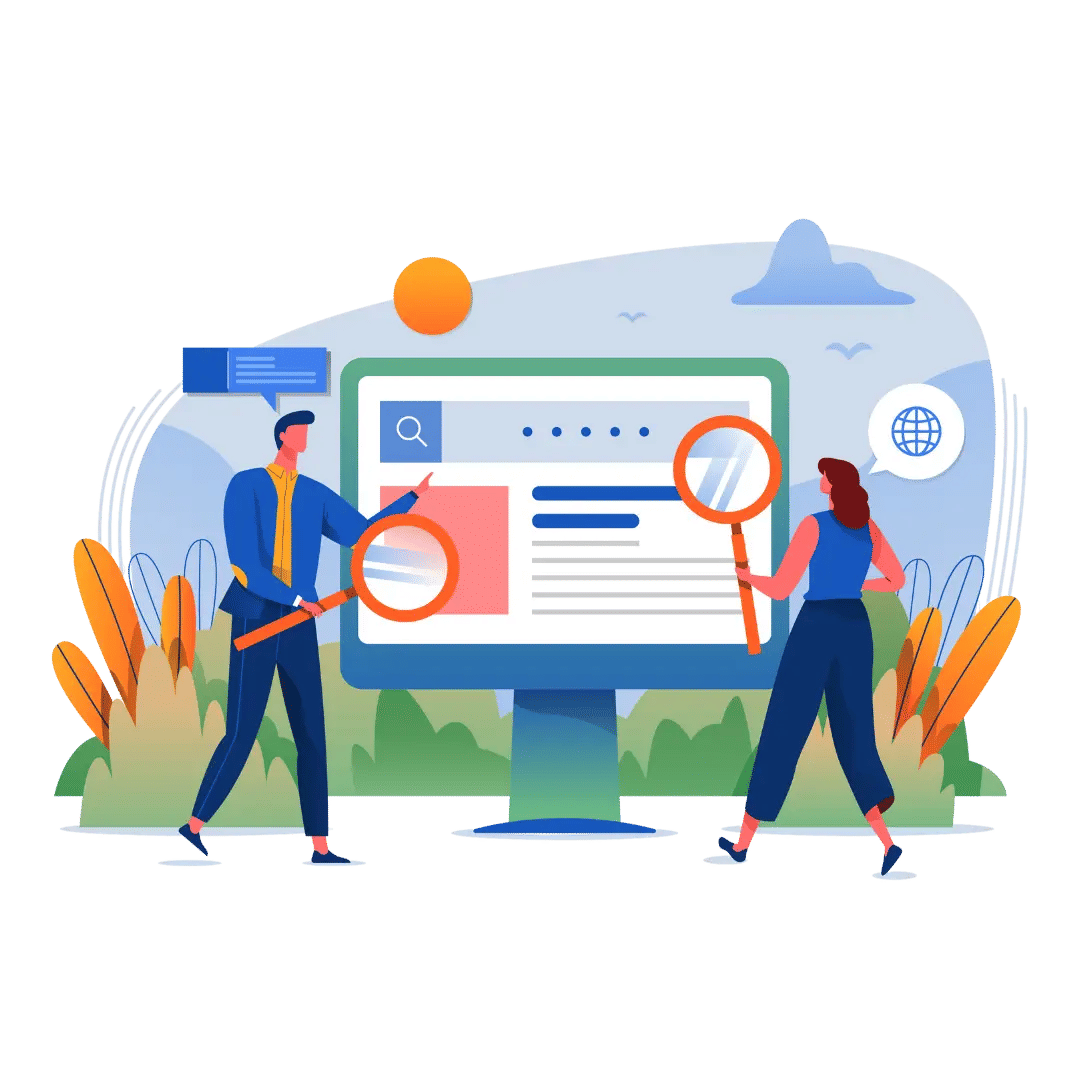
Enhancing the Experience in Onboarding Software for Manufacturing
Fostering Emotional and Psychological Adjustment
Starting a new job in manufacturing hr software onboarding can be overwhelming. Companies should help new hires adjust by fostering a sense of belonging through:
- Team-building exercises
- Regular check-ins with managers
- An open-door policy for addressing concerns
Emphasizing company culture, values, and mission helps employees connect their work to broader organizational goals.
Leveraging Technology for an Engaging Onboarding Process
Technology can make onboarding software for manufacturing more engaging and effective. Some useful tools include:
- Virtual Reality (VR) simulations for hands-on safety training
- E-learning modules for interactive policy and compliance training
- Mobile apps for quick access to workplace resources
These tools enhance consistency in knowledge transfer and make learning more interactive.
Incorporating Cross-Training for Workforce Flexibility
Cross-training employees early in their onboarding process helps them:
- Understand different aspects of production
- Increase adaptability in various roles
- Prepare for future career growth
A well-rounded workforce improves efficiency and operational flexibility.
Prioritizing Employee Health and Well-Being
Manufacturing jobs can be physically demanding. Companies should educate new hires on:
- Proper ergonomics and body mechanics
- Strategies to reduce fatigue and prevent injuries
- Wellness programs like stretching exercises and hydration reminders
A focus on well-being leads to healthier employees and fewer workplace accidents.
Equipping Supervisors to Support New Hires
Supervisors play a critical role in employee success. They should be trained to:
- Provide constructive feedback
- Recognize and reward employee achievements
- Offer ongoing coaching and mentorship
Strong leadership support enhances engagement, retention, and job satisfaction.
By incorporating these strategies, manufacturing companies can create a more effective onboarding process that boosts productivity, safety, and employee retention.
Building a Support System for New Employees
A strong support system is essential for helping new employees adjust, feel valued, and perform well in their roles. Without proper guidance, new hires may feel lost, leading to disengagement and higher turnover. Here’s how manufacturing hr software onboarding companies can create a structured support system:
1. Structured Onboarding Programs
A well-designed onboarding program helps new hires integrate smoothly. This should include:
- A detailed onboarding schedule outlining key training and milestones.
- Clear documentation of job roles, responsibilities, and company policies.
- Hands-on training and shadowing opportunities to build confidence.
2. Regular Check-ins with Supervisors
Frequent one-on-one meetings between new hires and supervisors ensure they are on track and comfortable. These check-ins should:
- Address any challenges or concerns early.
- Provide constructive feedback and recognition.
- Reinforce safety procedures and company values.
3. Encouraging Peer-to-Peer Support Networks
Creating an environment where employees can learn from one another strengthens teamwork. Ways to foster this include:
- Organizing small group discussions or lunch-and-learn sessions.
- Encouraging team collaboration on tasks and projects.
- Setting up internal chat groups for quick support and advice.
4. Establishing Open-Door Policies
New employees should feel comfortable approaching HR or leadership with any concerns. This can be supported by:
- Clearly communicating who they can turn to for help.
- Encouraging an open, feedback-driven culture.
- Creating an anonymous feedback system for employees to express concerns.
5. Providing Additional Resources
To ensure continuous learning and support, companies should offer:
- Employee handbooks and digital knowledge bases for easy reference.
- Access to training videos, FAQs, and safety guides.
- Onboarding surveys to gather feedback and make improvements.
A strong support system ensures that new employees feel welcomed, engaged, and prepared, leading to higher retention and better overall performance
Common Onboarding Challenges in Manufacturing
Even with a structured plan, challenges can arise. Here’s how to overcome them:
- High Turnover: Invest in mentorship programs and career growth opportunities.
- Safety Concerns: Reinforce safety training with regular refresher courses.
- Lack of Engagement: Make onboarding interactive with hands-on learning and team-building activities.
- Information Overload: Break down training into manageable sessions to avoid overwhelming new hires.
The Long-Term Benefits of Strong Onboarding
An effective onboarding for manufacturing program delivers long-term results, such as:
- Higher Employee Retention: Workers who feel prepared and supported are more likely to stay.
- Increased Efficiency: Well-trained employees contribute to faster production and fewer errors.
- Stronger Workplace Culture: A positive onboarding experience fosters teamwork and commitment.
- Better Compliance: Employees trained from the start follow regulations more consistently.
Conclusion
Onboarding for manufacturing is more than just a formality—it’s a crucial step in setting employees up for success. A well-planned process ensures safety, boosts productivity, and improves job satisfaction. Investing in proper onboarding benefits both employees and the organization, creating a stronger, more efficient workforce.
By utilizing an employee onboarding portal, manufacturing companies can streamline the training process, provide easy access to essential resources, and ensure consistency in onboarding procedures. This digital approach enhances efficiency, improves knowledge retention, and helps new hires integrate seamlessly into their roles.
By focusing on structured training, mentorship, and continuous learning, manufacturing companies can build a skilled, engaged, and loyal team.
Seamless Employee Onboarding
Onboard new hires faster, smarter, and with complete accuracy
Frequently Asked Questions
Why is onboarding important in manufacturing?
Onboarding in manufacturing ensures new employees quickly adapt to machinery, safety protocols, and productivity standards. It reduces errors, enhances workplace safety, and improves employee retention.
How does onboarding for manufacturing improve workplace safety?
Effective onboarding provides comprehensive safety training, covering equipment operation, PPE usage, emergency response, and hazard identification to prevent workplace accidents.
How does onboarding affect employee retention in manufacturing?
A structured onboarding program creates a supportive work environment, helping new hires feel valued and engaged. It reduces turnover by addressing concerns, offering mentorship, and providing career growth opportunities.
What are the key components of an effective onboarding for manufacturing?
A successful onboarding process includes pre-boarding preparation, safety training, job-specific training, mentorship, performance tracking, and ongoing learning opportunities.
How can technology improve the onboarding experience?
Technology like Virtual Reality (VR) simulations, e-learning modules, and mobile apps make onboarding interactive, ensuring consistent knowledge transfer and better engagement.
What are the biggest challenges in manufacturing hr software onboarding?
Common challenges include high turnover, safety concerns, lack of engagement, and information overload. Structured training, mentorship, and interactive learning help overcome these obstacles.
How can mentorship support new hires in onboarding for manufacturing?
Pairing new employees with experienced workers provides guidance, answers questions, and fosters a sense of belonging, helping them adjust faster.
How does onboarding software for manufacturing help with compliance in manufacturing?
Onboarding Software for Manufacturing ensures employees understand industry regulations, company policies, and safety standards, reducing legal risks and ensuring compliance.