LMS for Manufacturing: Revolutionize Employee Training
LMS for Manufacturing streamlines employee training, enhancing productivity, compliance, and skill development for a more efficient and skilled workforce.
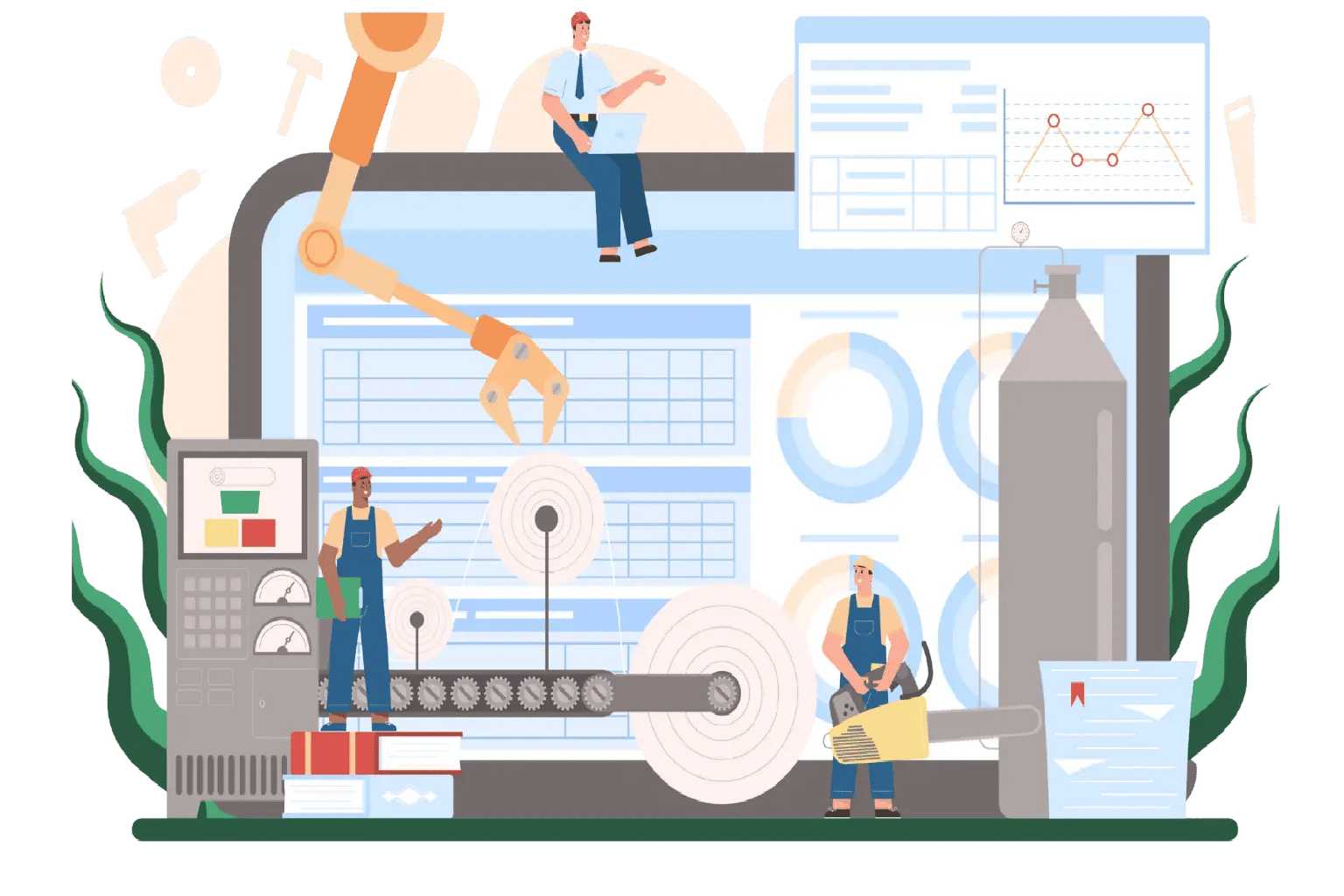
Training employees in the manufacturing sector is vital for staying ahead of the competition, improving operational efficiency, and maintaining safety standards. A Learning Management System (LMS) for manufacturing companies provides a central platform to streamline and improve this training process, making it more effective, efficient, and engaging.
Manufacturing industries are increasingly adopting LMS platforms to manage employee training and performance. With the right LMS in place, companies can reduce training time, boost workforce engagement, and enhance compliance. By creating an integrated learning environment, manufacturing businesses can address their specific training needs in an effective manner, whether for safety procedures, skills development, or operational training.
What Is LMS for Manufacturing?
An LMS for manufacturing is a software platform designed to manage, track, and deliver training programs to employees in the manufacturing sector. It allows businesses to automate training, monitor progress, and ensure compliance with industry regulations. The system can deliver training content, manage certifications, and track employee performance, all while being accessible remotely.
LMS provides a structured learning experience, guiding learners step by step. It keeps them on track, ensuring smooth progress and consistent engagement, like a personal mentor. For example, manufacturing workers can access training modules on equipment safety, machinery maintenance, or production protocols, all tailored to their roles within the company. With mobile accessibility, training can occur on the factory floor or from anywhere, making it convenient for employees to learn without disrupting production.
Why LMS for Manufacturing Is Important
The importance of LMS in manufacturing cannot be overstated. Here are a few key reasons why:
- Improves Employee Skills: An LMS ensures that employees have the right skills to perform their jobs. Whether it’s technical expertise or safety protocols, workers need continual training to improve their knowledge and stay current with industry standards.
- Increases Efficiency: LMS eliminates traditional manual training methods, like printed manuals and in-person workshops, which can be slow and inefficient. Through automated workflows, employees receive timely training, allowing them to quickly become proficient in their roles.
- Enhances Safety and Compliance: The manufacturing sector has strict safety regulations. With LMS, businesses can provide ongoing training on safety standards and ensure that employees are up to date on the latest compliance regulations.
- Standardizes Training: LMS ensures that all employees receive the same training experience, helping to eliminate discrepancies in skills or knowledge across teams and departments.
- Boosts Employee Engagement
LMS platforms provide interactive learning experiences, which can include quizzes, simulations, and gamification. These elements increase employee engagement, making training more enjoyable and encouraging employees to stay committed to their learning journey.
- Facilitates Remote and On-the-Go Learning
With mobile compatibility, an LMS lets employees learn on their own terms whether they’re at home, on the go, or in the office. It gives them the freedom to access training materials whenever it’s most convenient, making learning flexible and adaptable to their busy lives. This flexibility is especially important for manufacturing workers who may be in the field or working in areas with limited access to traditional learning tools.
- Streamlines Performance Tracking and Reporting
LMS systems provide real-time tracking of employee progress. Managers can effortlessly track progress by monitoring completion rates, scores, and skill growth. This visibility allows them to stay informed on how their team is developing, making it easier to offer support and celebrate milestones along the way. This data is invaluable for identifying areas for improvement and ensuring that employees are meeting required benchmarks.
- Reduces Training Costs
By digitizing training materials and eliminating the need for in-person trainers or travel expenses, LMS reduces training costs. Companies can save money while still providing high-quality, standardized training to a large workforce.
- Enhances Knowledge Retention
LMS platforms typically include features like spaced learning and assessments that help reinforce training content. This method has been shown to improve long-term knowledge retention, ensuring that employees can recall crucial information when it matters most.
Best LMS for Manufacturing Industry
When selecting the best Learning Management System (LMS) for the manufacturing industry, it’s crucial to choose a platform that supports specific training needs, such as compliance, safety protocols, skills development, and operational efficiency. The right LMS should streamline training processes, enhance employee engagement, and ensure that workers are equipped with the skills needed to perform their tasks effectively and safely.
Here are some of the best LMS platforms specifically tailored for the manufacturing industry:
- LMS 365
LMS 365 is a learning management system for the manufacturing industry, seamlessly integrating with Microsoft 365. It offers mobile access, customizable workflows, and robust reporting tools. LMS 365 enhances operational efficiency, safety compliance, and onboarding, supporting both in-person and remote learning. It tracks employee progress to maintain high training standards across the workforce, and ensures alignment with industry regulations and standards.
- TalentLMS
TalentLMS is user-friendly and scalable, ideal for manufacturers who need to deliver training across multiple devices. Its reporting features and integration options help track employee progress efficiently. With an intuitive interface, it simplifies the onboarding process and enhances the overall user experience.
- Docebo
Docebo offers a robust, AI-powered platform that personalizes learning for employees, ensuring they receive the right training at the right time. It supports blended learning for better workforce engagement, and its analytics features help businesses measure the effectiveness of training programs and drive continuous improvement.
- Litmos
Litmos excels in compliance training, a critical requirement in the manufacturing sector. Its user-friendly interface, comprehensive reporting tools, and ability to handle both safety and operational training make it ideal for this industry. The platform also provides automated reminders and alerts, ensuring employees stay on track with their training milestones.
- WorkRamp
WorkRamp offers customizable solutions for safety, compliance, and skills training in manufacturing. It also integrates well with business tools, ensuring a smooth workflow. Its collaborative features encourage team participation, enhancing learning engagement across departments.
- GyrusAim
GyrusAim is tailored for complex organizations, such as manufacturers, offering a blend of e-learning and instructor-led training. It offers robust tools for tracking compliance and generating reports, helping ensure that all required training is completed on time. This makes it easier for managers to stay on top of regulations and maintain accountability across the team. Additionally, its scalability ensures that the system grows with your company’s needs, allowing for the seamless addition of new users and training materials.
By adopting an LMS like LMS 365, manufacturers can not only streamline their training processes but also improve employee engagement, compliance, and overall workforce efficiency. This leads to enhanced productivity, reduced risks, and better-trained employees who are ready to meet the demands of the manufacturing environment.
LMS for Manufacturing: Revolutionize Employee Training from Day One to Excellence
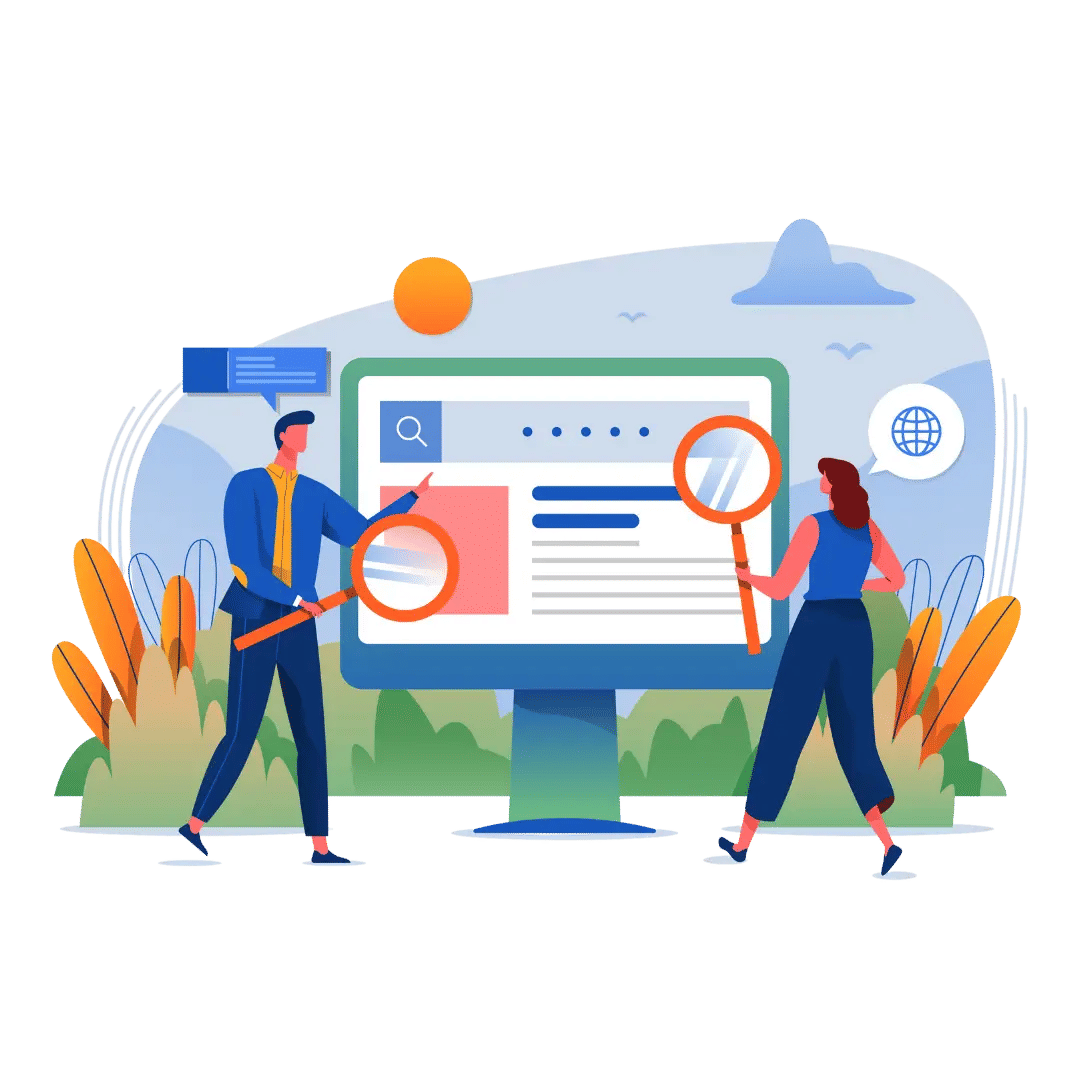
Key Benefits of LMS for Manufacturing
The introduction of an LMS in manufacturing can transform the entire training process. Here are some core benefits:
Improved Employee Engagement
- An LMS increases employee engagement by offering personalized learning experiences. Employees stay more engaged when they see how training directly connects to their current roles and future career growth. When the learning feels purposeful, it sparks a deeper sense of motivation and investment in their development.
- Interactive training content, such as videos and quizzes, enhances engagement and helps employees retain information.
Faster Onboarding
- Onboarding new employees in manufacturing can be slow if done manually. An LMS accelerates the onboarding process by providing structured training and clear pathways for new hires to follow.
- It ensures that new employees receive all necessary training on equipment, safety standards, and job responsibilities from the very first day, without overwhelming them.
Cost Savings
- Traditional training methods can be costly, especially if they involve bringing in external trainers or organizing in-person workshops. An LMS allows companies to deliver training remotely, saving on travel and accommodation costs.
- Furthermore, it reduces the need for re-training, as employees can access training materials anytime, they need a refresher.
Better Compliance Tracking
- In industries like manufacturing, staying on top of safety regulations isn’t just important it’s essential. Compliance ensures a safe work environment, protects employees, and helps businesses avoid costly setbacks, all while maintaining trust and credibility. An LMS helps track employee progress, certifications, and training completion, ensuring that companies comply with industry standards.
- It provides audit-ready documentation of employee training records, which is essential for compliance during inspections.
Scalability
- As manufacturing companies grow, the need for effective training systems increases. LMS platforms grow with your needs, easily adding more users and training programs without the hassle of major system overhauls. This flexibility allows businesses to expand and adapt as they evolve, keeping learning streamlined and efficient.
- Whether your company has 50 employees or 5,000, an LMS ensures consistent training delivery across all locations.
Enhanced Employee Retention
Offering continuous learning and development opportunities through an LMS can significantly boost employee retention. When employees see that their employer is committed to helping them grow, it fosters a sense of loyalty. Investing in their development shows you care about their future, which strengthens their connection to the company and boosts long-term retention.
Regular training and career development initiatives increase job satisfaction and foster a culture of continuous improvement, making employees feel valued and motivated to stay long-term.
Features of an LMS for Manufacturing
The best LMS platforms for manufacturing industries come with features that address the specific needs of the sector. Here are some features to look for:
Mobile Accessibility
- Manufacturing workers are often on the move or working in areas with limited access to computers. A mobile-compatible LMS ensures that employees can access training materials on their smartphones or tablets.
- This feature allows workers to complete training sessions on the go, even while on the factory floor.
Customization
- Each manufacturing company has its own set of processes, machinery, and equipment. An LMS should allow for customization to create training programs specific to your company’s needs.
- From training materials on specific machinery to safety protocols, a customizable LMS ensures that the learning experience aligns with the company’s goals.
Real-Time Tracking
- With real-time progress tracking, managers can see how well employees are performing in their training. If a worker is struggling with a certain task, training can be adjusted accordingly.
- This feature also allows for the management of certifications, ensuring that employees stay up-to-date with required courses and qualifications.
Interactive Content
- LMS platforms can offer a variety of interactive learning materials such as videos, simulations, and gamified content. This approach makes training more interactive, capturing employees’ attention and improving how well they absorb and remember the material. It transforms learning into something meaningful, making it easier to retain and apply what they’ve learned.
- For example, machinery training might include interactive simulations that allow workers to safely practice operating equipment without any risk.
Reporting and Analytics
- LMS systems provide detailed reports on employee progress, certifications, and performance. This data can be used to identify areas where employees may need further training or to monitor the effectiveness of training programs.
- With this data, managers can make informed decisions on employee development and improve overall training programs.
Trends Shaping the Future of LMS in Manufacturing
The future of LMS in manufacturing is constantly adapting, finding new ways to meet the industry’s changing needs. As technology advances, these platforms are becoming more intuitive and tailored, ensuring that training keeps pace with innovation and workplace demands.
AI and Machine Learning
- Artificial intelligence (AI) is playing an increasingly important role in personalizing the learning experience. AI-driven LMS can adapt training based on individual progress and predict areas where employees may need further training.
- Machine learning algorithms can also identify patterns and suggest targeted training materials for employees, improving efficiency and learning outcomes.
Virtual Reality (VR) and Augmented Reality (AR)
- VR and AR are making their way into manufacturing training. These technologies can simulate real-world scenarios, such as operating heavy machinery or navigating factory layouts, in a controlled, risk-free environment.
- With VR and AR, manufacturing companies can create hands-on training experiences that are immersive and realistic, offering scenarios that would be too costly or complex to replicate in real life. This technology brings learning to life, making it safer and more effective for employees.
Microlearning
- Microlearning focuses on delivering small, bite-sized chunks of training that employees can complete in short periods. This trend is gaining traction in the manufacturing sector as it fits into the busy schedules of workers.
- It’s ideal for providing just-in-time training, where workers can access quick tutorials or refreshers on specific tasks right before performing them.
Social Learning and Collaboration
- Many modern LMS platforms now include social learning features, enabling employees to exchange knowledge, collaborate on training modules, and connect with colleagues. This fosters a sense of community and enhances learning through shared experiences.
- This fosters a community learning environment and helps employees learn from each other’s experiences and expertise.
Conclusion
Investing in an LMS for manufacturing can have a profound impact on employee engagement, productivity, and long-term success. With its ability to streamline training, ensure compliance, and reduce costs, an LMS is an essential tool for manufacturers looking to stay competitive in an ever-evolving industry.
By adopting a tailored LMS for manufacturing, companies can provide their employees with the resources they need to succeed in their roles while improving overall operational efficiency.
Book a Demo:
Ready to optimize your employee training with LMS for manufacturing? Book a demo of LMS 365 today and see how it can transform your workforce training.
Empower Your Manufacturing Team
Transform your training process with LMS software that enhances skills development, boosts safety compliance, and accelerates employee productivity from day one.
Struggling to hire great professionals?
A strong recruitment marketing strategy wins hearts, builds trust, and fills roles before your competitors even blink.
Frequently Asked Questions
What is LMS for manufacturing?
An LMS for manufacturing is a software tool designed to automate, track, and deliver training programs to employees, ensuring they have the necessary skills and knowledge to perform their jobs effectively. This system helps streamline training efforts and maintain consistency across all levels of the workforce.
How does LMS benefit manufacturing companies?
LMS benefits manufacturing companies by improving training efficiency, increasing employee engagement, ensuring compliance, and reducing the time and cost associated with traditional training methods. It also enhances the overall productivity of employees by providing real-time access to learning resources.
Can LMS be used for remote manufacturing workers?
Yes, LMS platforms are mobile-friendly and can be accessed from anywhere, making them ideal for remote or hybrid manufacturing workforces. This flexibility ensures that employees can complete training modules at their convenience, regardless of their location.
How does LMS help with compliance in manufacturing?
LMS platforms help manufacturing companies ensure that all employees complete required training and certifications, keeping the company compliant with industry regulations. Automated reminders and tracking ensure that employees do not miss important training deadlines.
What features should I look for in an LMS for manufacturing?
Look for features such as mobile accessibility, real-time tracking, customizable workflows, interactive content, and integration with HR systems to maximize the effectiveness of your LMS. These features ensure that training is efficient, engaging, and aligned with your company’s goals.